华南区域销售工程师
电话:
13718662690(李绍宏)
邮箱:
lsh@jyhypower.cn
江苏区域销售工程师
电话:
13333738312(张静宇)
邮箱:
zjy@jyhypower.cn
山东区域销售工程师
电话:
15811186903(高荣彪)
邮箱:
grb@jyhypower.cn
华北区域销售工程师
电话:
15617665003(贾豪星)
邮箱:
jhx@jyhypower.cn
华东区域销售工程师
电话:
13333738312(张静宇)
邮箱:
zjy@jyhypower.cn
西南区域销售工程师
邮箱:
qhj@jyhypower.cn
售后工程师
电话:
13771158250(孙文静)
邮箱:
swj@jyhypower.cn
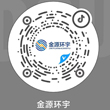
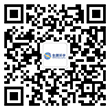